Welding is one of the manufacturing processes where two or more materials can be joined permanently through coalescence formation with or without the application of external heat, pressure, or filler metal. Welding processes can be broadly classified as fusion welding and solid state welding. In fusion welding processes, significant amount of heat (thermal energy) is applied from external source in order to fuse (melt) the faying surfaces of the components that are to be joined. Such heat can be applied through electric arc, electrical resistance, exothermic reaction, or highly intense beam of laser, plasma, or electrons. On the contrary, in solid state welding processes, heat is usually not applied from external sources, or even if small amount heat is applied then the components are not allowed to melt. So joining is carried out in solid state without any phase change (from solid to liquid). Instead of heat, usually external pressure is applied in such welding processes. Whatever be the case, a coalescence or weld bead forms in the welded samples along the junction.
In fusion welding, a portion of the base metals surrounding the junction is melted and re-solidified. This zone around the junction that melts and re-solidifies is called weld metal (or weld bead). Thus weld metal changes its phase (solid to liquid and once again liquid to solid) to form coalescence. Filler metal, if added, also melts and deposits on the joint to finally become a part of the weld metal. Thus weld metals are always heated above the melting temperature of the concerned material. Accordingly, entire material of the weld metal is subjected to excessive heating, melting, liquid-state-mixing, and finally solidification. Microstructures and mechanical properties of the weld metal can be significantly different from that of the parent components. Typically weld metal geometry is characterized by three dimensional parameters, namely penetration depth, weld bead width, and reinforcement. Such parameters depend on a large number of factors such as type of welding process, extent of heat applied, workpiece material properties, etc. While the weld metal zone is conspicuously noticeable in fusion welding process, the same is narrow in solid state welding processes owing to the absence of melting.
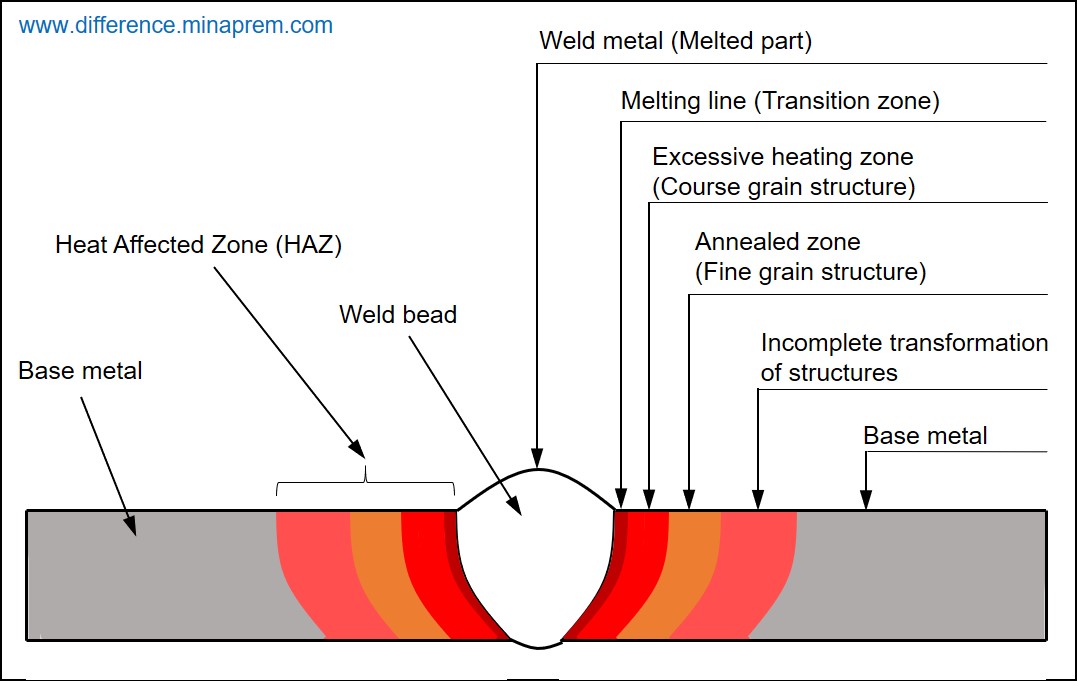
Heat Affected Zone (HAZ) is a part of the base metal that is not melted during the fusion welding but is heated to an elevated temperature (below the melting temperature of the concerned material) before cooling down to room temperature. HAZ is located surrounding the weld metal. HAZ does not contain filler metal. Base metal within the HAZ undergoes heating and subsequent cooling; however, no phase change occurs (that means HAZ always remains in solid phase). Owing to the thermal cycle, metallurgical and mechanical properties of the HAZ can vary significantly from that of the base metals. However, the chemical composition matches with that of the base metal (excluding composition change owing to small scale of diffusive atom transfer). HAZ geometry is usually defined by its width only. HAZ width, once again, varies with the welding process, selected parameters, extent of heating, base metal properties, number of passes, etc. While HAZ width is significant in fusion welding, it is mostly negligible in solid state welding processes.
While both weld metal and HAZ are integrated part of every welded joint, their characteristics vary depending upon a large number of features and conditions. Both the parts are subjected to thermal cycle and thus are susceptible to undesired residual stress and cracking. While the weld metal properties can be altered during welding by suitably choosing filler composition, shielding composition, etc., the same is not feasible for HAZ. Strength of the weld metal mostly remains 100% (if not more) of the strength of the base metal. However, HAZ region is relatively more vulnerable to fail early during service life. Thus utmost care is given during welding, especially arc welding, to maintain HAZ width and its properties within tolerable limit. Various similarities and differences between the weld metal and Heat Affected Zone (HAZ) of a welded joint are given below in table format.
Similarity between weld metal and HAZ
- Several physical, mechanical and metallurgical properties of both the weld metal and HAZ are affected due to thermal cycle.
- Both are integrated part of a welded joint. In fusion welding, both are conspicuously noticeable. However, in solid state welding, they are usually narrow.
- Strength and quality of weld joint is dependent on the quality of both the weld bead and HAZ.
Difference between weld metal and HAZ
Weld Metal | Heat Affected Zone (HAZ) |
---|---|
Weld metal is usually treated as a separate part in the welded sample, rather than considering it as a part of the base metal. | HAZ is usually considered as an integrated part of the base metal. |
Weld metal region exists at the junction of two parent components. | HAZ exists within the parent components surrounding the weld bead. |
In fusion welding, weld metal undergoes phase change due to meting and subsequent solidification (solid to liquid and once again liquid to solid). | HAZ is never melted. It always remains solid. So no phase change occurs in HAZ. |
It contains significant portion of filler material (except in autogenous welding). | It does not contain any filler material. It is purely a part of the base materials. |
Chemical composition of weld bead may differ from that of the parent metals. | Chemical composition of HAZ is mostly same with that of the parent metals. |
Properties of the weld metal can be improved during welding in several ways (such as appropriately selecting filler composition, shielding gas, etc.). | Properties of the HAZ cannot be improved favourably during welding (its width can only be controlled to some extent). |
Weld bead produces in both fusion welding and solid state welding processes. However, it is narrow in solid state welding. | HAZ is noticeable particularly in fusion welding processes. With solid state welding, HAZ is very narrow and is mostly not detectable. |
Geometry of the weld metal is characterised by three parameters, namely (i) depth of penetration, (ii) weld bead width, and (iii) reinforcement height. | Only geometrical parameter of interest of the HAZ is its lateral width. |